top of page
Mechanical xylophone
creative mechanical design, engineering, and manufacturing
Assignment
"Create an artistic chain reaction machine utilising engineering techniques such as the finite element analysis (material stress simulation in CAD) and designing for sustainable and financially efficient manufacturability."
Learning Points
-
Consideration of engineering requirements, manufacturing machinery, and costs of mass manufacture.
-
Material stress test simulations in order to make decisions on material
-
Advanced prototyping machines (laser-cutting, 3D printing of flexible material).

Process
inspiration

The concept
See-saw system with elastic bands to let the hammers in the middle strike the xylophone bars, which would be mounted on top.
A second iteration reversed the mechanism — gravity would do the work of striking the bars, and they would be mounted on the bottom

Product goals
1. Play multiple xylophone bars (>= 4)
2. Be fully manual (no electronics)
3. Be programmable (comparable to a ‘book organ’)
Digital prototype 1

Manufacturing: very early in the design stage: cost and material optimization were paramount, as part of the brief was to create a mechanically and financially efficient design
Assembly: how were the frame, the cylinder, the hammers, the xylophone, and the pegs to fit together?
We broke the design task into 6 parts: hammer, peg, handle, cylinder, xylophone,frame/assembly — to design their individual forms in detail.
handle and cylinder
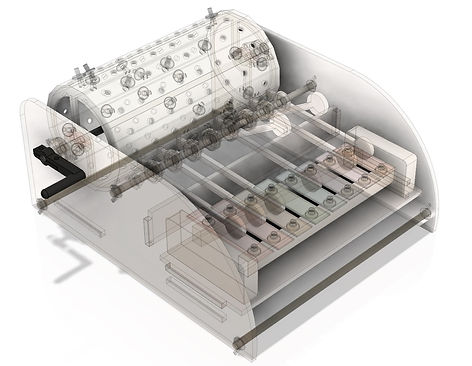
The handle is used to rotate the cylinder. To attach the handle to the rotating rod, a force
constraint is used.
This constraint aims to limit all degrees of freedom, except for one rotational axis (around the rod).
To create this force constraint, the handle is split into two parts.
These parts can be tightened together using bolts


The clamp used to attach the cylinder to the rod is similar to the force constraint used for the handle.
The bottom side of the clamp is part of the form of the cylinder, while the
top part is printed separately.
The cylinder has 16 faces in order to create a repeating 16-beat melody in 4/4 by manually spinning it with the handle.

Hammer

There are 8 hammers made out of medium-density fiberwood (MDF).
The hammers act as
levers, with a hole at the tail to mount a metal rod though.
The other side has a
hammerhead which strikes the xylophone bars.

The hammers are pushed upon by the pegs. To make sure that the pins can withstand the opposing force, calculations were made to estimate the force put on the pins by the hammers.

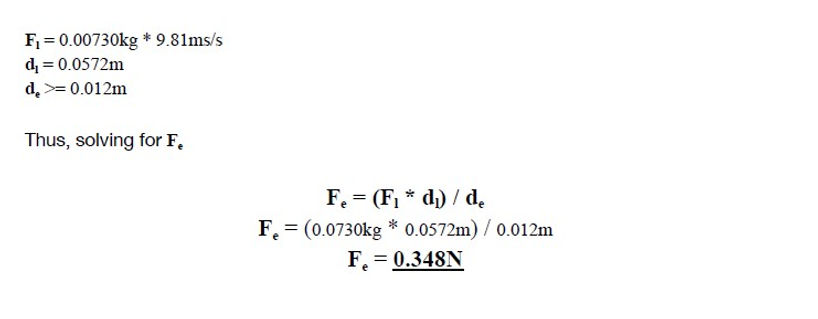
This means that the pegs needs to be able withstand 0.348N of force, as the upper bound.

nut
hammer
spring
To constrain the hammers in the horizontal direction, a solution includes applying a constant elastic force onto one side of the hammer, pinning it to the nut on its other side.
That way, the hammer’s movement in the unwanted horizontal direction is minimized, and it will consistently strike the xylophone.
Peg
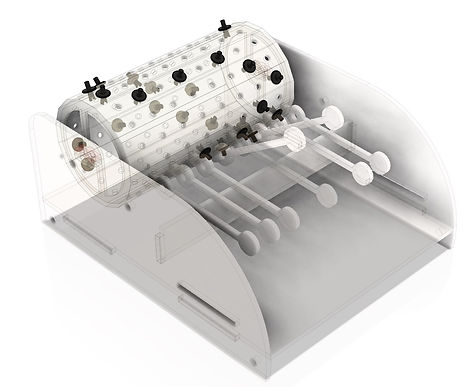
By placing/removing pegs, users can decide if a note should be played on a per beat basis.
Requirement: they should be easily placable and removable by the user.

The legs of the pegs need to be able to withstand enough force so that they can be squished together by the user to place into a hole onto the cylinder, where they will bend back outwards to hold themselves in place.
Finite element analysis

The maximum principal stress analysis shows that the maximum stress applied to the peg using 90N of max male pinch strength is 86.23MPa.
The Yield Strength of ABS plastic is 20MPa. Conclusively, the finite element analysis predicts that the part is likely to break.
Through the finite element analysis, we determined that we need to use a material with high yield and a higher fracture threshold.
Luckily, the university 3D printer can print using a softer PLA filament, which allows the legs of the peg to be bent further without the risk of fracture.

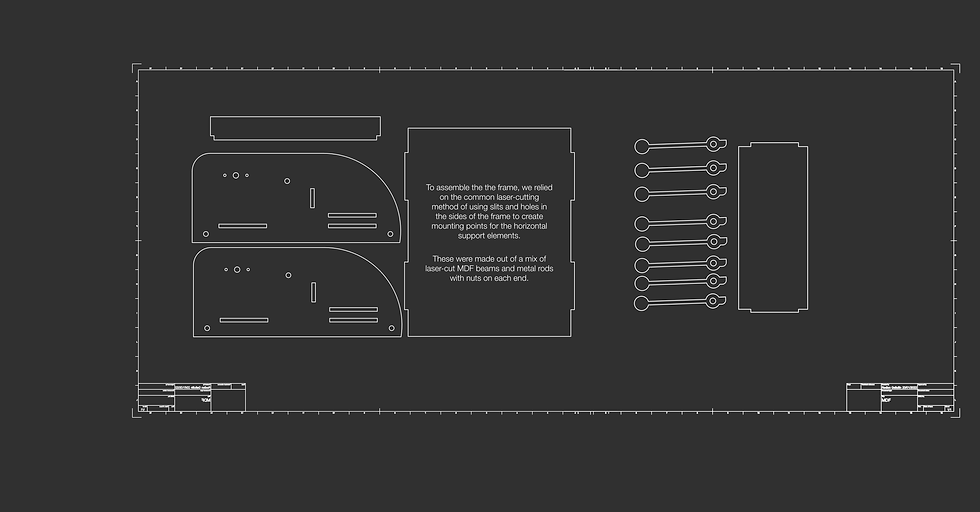
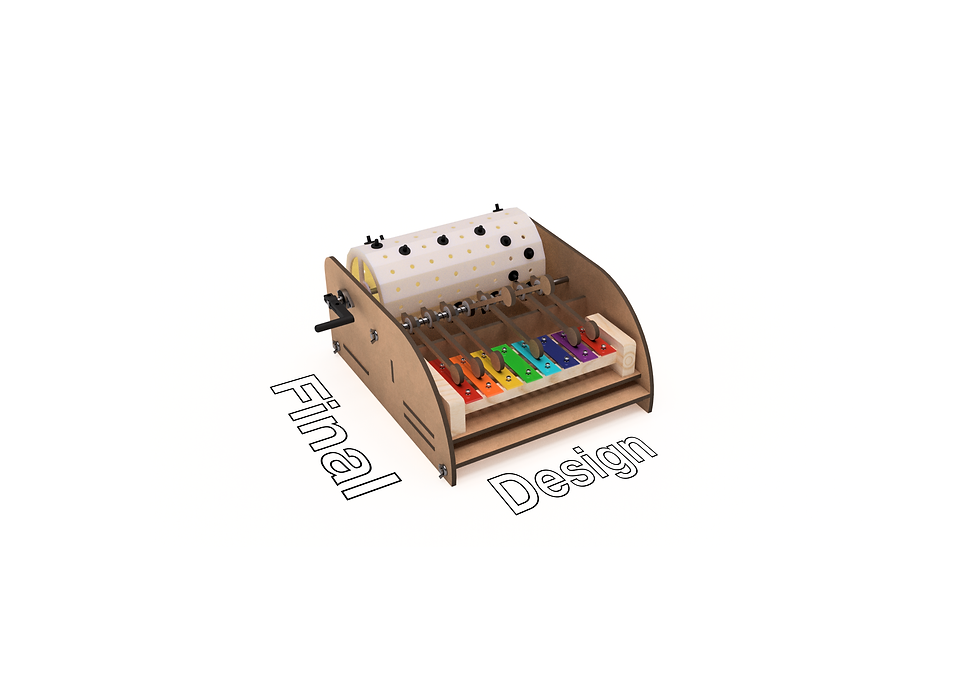
Cost of manufacturing & Bill of materials
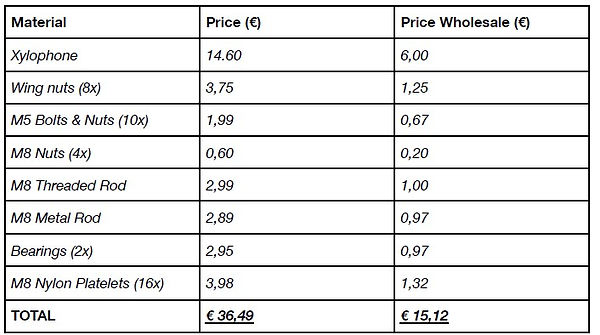

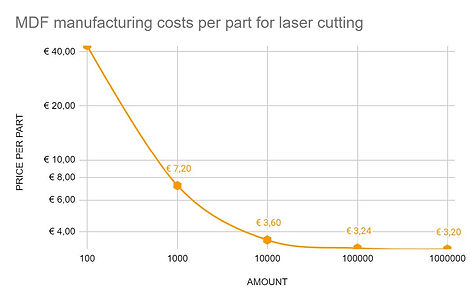
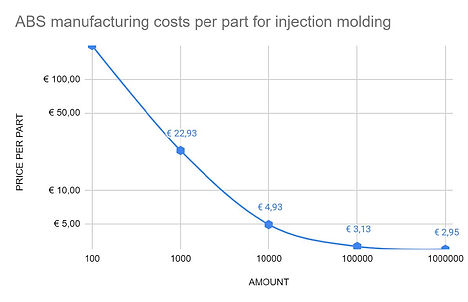

While the 3D parts in the prototype were 3D printed, it’s rare for mass-produced products to be 3D printed. This is mainly due to the slow speed of 3D printing, and additive layer manufacturing in general. Components that get 3D printed in the rapid prototyping phase, often get injection molded in production. The constant costs associated with injection molding are generally higher. The act of injection molding gets outsourced quite often on medium scale projects, since the machinery needed is highly expensive. When outsourcing the injection molding, consumers only need to pay for the creation of a mold. This dramatically lowers the constant costs associated.
bottom of page